A quick summary and overview
Pallet racking is a cornerstone of modern warehouse management, offering versatile storage solutions that maximize space utilization and operational efficiency. This comprehensive guide explores various pallet racking types, crucial safety considerations, and integration with inventory systems. We’ll delve into the economic benefits of well-implemented racking solutions and address common challenges faced by warehouse managers. With insights from MacMillan Supply Chain Group, you’ll learn how to select, implement, and maintain the ideal pallet racking system for your unique needs, ultimately driving productivity and cost savings in your supply chain operations.
An introduction
In today’s fast-paced logistics landscape, optimizing warehouse space and enhancing operational efficiency are paramount for businesses looking to stay competitive. Pallet racking systems stand at the forefront of this optimization, offering a structured approach to vertical storage that can dramatically increase capacity and streamline workflows. Whether you’re managing a small distribution center or overseeing a massive fulfillment operation, the right pallet racking solution can be a game-changer for your business.
At MacMillan Supply Chain Group, we understand that choosing the perfect racking system involves balancing numerous factors, from inventory turnover rates to safety regulations. This guide aims to demystify the world of pallet racking, providing you with the knowledge to make informed decisions that will propel your warehouse operations to new heights of efficiency and productivity.
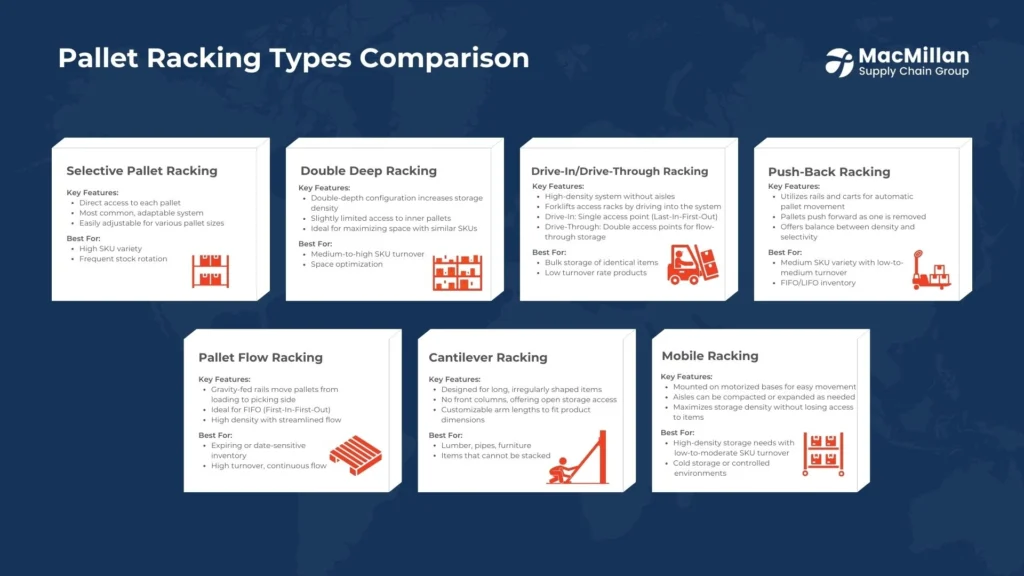
Types of Pallet Racking Systems
Pallet racking systems come in various configurations, each designed to meet specific warehouse needs and inventory profiles. Understanding these types is crucial for selecting the optimal solution for your operation:
- Selective Pallet Racking: The most common and versatile option, offering direct access to every pallet. Ideal for warehouses with a wide variety of SKUs and frequent stock rotation.
- Double Deep Racking: Similar to selective racking but with double depth, increasing storage density at the cost of slightly reduced accessibility.
- Drive-In/Drive-Through Racking: High-density storage solution perfect for bulk storage of homogeneous products with low turnover rates.
- Push-Back Racking: Utilizes inclined rails and carts to automatically push pallets forward when the front pallet is removed, combining density with good selectivity.
- Pallet Flow Racking: Gravity-fed system that automatically moves pallets from loading to picking side, ideal for FIFO (First-In-First-Out) inventory management.
- Cantilever Racking: Designed for long or irregularly shaped items, featuring arms extending from the uprights to support loads without front columns.
- Mobile Racking: Mounted on motorized bases, these systems can be compacted to eliminate aisles when not in use, maximizing storage density.
At MacMillan Supply Chain, we help you navigate these options, considering factors like your inventory characteristics, picking frequency, and available space to recommend the most suitable racking system for your warehouse.
Safety Considerations and Maintenance
Ensuring the safety and longevity of your pallet racking system is critical for protecting your inventory, employees, and bottom line. Here are key safety considerations and maintenance practices:
- Regular Inspections: Conduct thorough visual checks weekly and professional inspections annually to identify damage, wear, or misalignment.
- Load Capacity Compliance: Strictly adhere to manufacturer-specified weight limits for each rack and beam level to prevent structural failures.
- Proper Installation and Assembly: Ensure racking is installed by certified professionals following manufacturer guidelines and local building codes.
- Employee Training: Provide comprehensive training on safe loading/unloading procedures, forklift operation, and identifying potential hazards.
- Protection Accessories: Install column protectors, end-of-aisle guards, and wire mesh decking to prevent damage and enhance safety.
- Clear Aisle Maintenance: Keep aisles free of obstructions and ensure proper lighting for safe navigation.
- Immediate Repair Protocol: Address any damage or wear immediately to prevent escalation of safety risks.
- Documentation: Maintain detailed records of inspections, repairs, and modifications for compliance and tracking purposes.
- Load Placard Display: Clearly display maximum load capacities on each rack for easy reference.
- Seismic Considerations: In applicable regions, ensure racking meets seismic safety standards.
MacMillan Supply Chain offers comprehensive safety audits and maintenance programs to keep your racking systems in optimal condition, minimizing risks and maximizing operational uptime.
Integration with Inventory Management Systems
Seamless integration between pallet racking and inventory management systems is crucial for optimizing warehouse operations. This synergy enhances accuracy, efficiency, and visibility across your supply chain. Here’s how to achieve effective integration:
- Barcode and RFID Technology: Implement scanning systems for real-time tracking of pallet locations and movements within the racking system.
- Warehouse Management Software (WMS): Utilize advanced WMS that can map your racking layout and optimize picking routes based on inventory locations.
- Automated Storage and Retrieval Systems (AS/RS): For high-volume operations, consider integrating automated systems that work in tandem with your racking for faster, more accurate picking and putaway.
- IoT Sensors: Deploy sensors on racking to monitor environmental conditions, load weights, and structural integrity, feeding data into your management systems.
- Digital Twin Technology: Create a virtual replica of your warehouse layout, including racking configurations, to simulate and optimize operations.
- Mobile Devices: Equip staff with handheld devices that interface with your inventory system for on-the-spot updates and location verification.
- Data Analytics: Leverage big data analytics to identify trends, optimize stock placement, and predict maintenance needs based on usage patterns.
MacMillan Supply Chain specializes in integrating cutting-edge inventory management technologies with pallet racking systems, ensuring your warehouse operates at peak efficiency. Our solutions are tailored to your specific needs, providing a seamless flow of information from rack to stock.
Economic Benefits of Optimized Pallet Racking
Implementing a well-designed pallet racking system can yield significant economic advantages for your business:
- Space Optimization: Maximize vertical storage space, potentially reducing the need for warehouse expansion or additional facilities.
- Improved Inventory Turnover: Efficient organization leads to faster stock rotation, reducing holding costs and improving cash flow.
- Enhanced Labor Productivity: Well-organized racking systems reduce picking times and improve order fulfillment rates, increasing overall workforce efficiency.
- Reduced Damage and Losses: Proper storage minimizes product damage, decreasing write-offs and insurance claims.
- Lower Operating Costs: Optimized layouts reduce equipment travel distances, lowering fuel costs and equipment wear.
- Increased Storage Capacity: Vertical expansion can increase storage capacity by up to 50% without expanding floor space.
- Flexibility for Growth: Modular racking systems allow for easy reconfiguration as business needs evolve, avoiding costly renovations.
- Improved Safety: Fewer accidents mean reduced workers’ compensation claims and less downtime.
- Energy Efficiency: Better organization can lead to reduced lighting and HVAC needs in certain areas of the warehouse.
- Enhanced Customer Satisfaction: Faster, more accurate order fulfillment improves customer experience and loyalty.
MacMillan Supply Chain’s expertise in pallet racking optimization helps businesses realize these economic benefits, offering tailored solutions that drive profitability and operational excellence.
Common problems with the topic
Our solutions
While pallet racking systems offer numerous benefits, warehouses often encounter challenges in their implementation and use. Here are common problems and MacMillan Supply Chain’s innovative solutions:
Problem: Inefficient Space Utilization
Solution: We conduct comprehensive space analysis using advanced 3D modeling software to design layouts that maximize every cubic foot of your warehouse. Our experts consider factors like inventory profiles, picking frequencies, and equipment specifications to create a customized racking layout that optimizes space utilization.
Problem: Safety Concerns and Accidents
Solution: MacMillan implements a multi-faceted safety approach, including regular safety audits, installation of protective equipment (like rack guards and safety netting), and comprehensive staff training programs. We also offer cutting-edge IoT-enabled safety monitoring systems that alert managers to potential hazards in real-time.
Problem: Difficulty in Inventory Management
Solution: We integrate smart racking solutions with advanced Warehouse Management Systems (WMS) to provide real-time inventory visibility. Our RFID-enabled racking systems allow for automated tracking, reducing errors and improving stock accuracy.
Problem: Inflexibility to Changing Business Needs
Solution: MacMillan designs modular racking systems that can be easily reconfigured or expanded. We also offer hybrid solutions that combine different racking types, allowing for adaptability as your inventory profile changes.
Problem: High Maintenance and Repair Costs
Solution: Our preventive maintenance programs use predictive analytics to identify potential issues before they become costly problems. We also offer durable, high-quality racking materials and protective accessories that reduce wear and tear, minimizing long-term maintenance costs.
Problem: Slow Order Fulfillment
Solution: MacMillan implements advanced slotting optimization strategies, placing fast-moving items in easily accessible locations. We also design pick paths that minimize travel time and integrate with automated picking systems where appropriate.
Problem: Environmental Concerns
Solution: We offer eco-friendly racking options made from recyclable materials and design systems that reduce energy consumption through optimized layouts and integration with energy-efficient lighting and HVAC systems.
Problem: Difficulty in Managing Seasonal Inventory Fluctuations
Solution: Our dynamic racking solutions, such as push-back or pallet flow systems, allow for easy adjustment to seasonal changes. We also provide temporary storage solutions and consult on inventory management strategies to handle peak periods efficiently.
By partnering with MacMillan Supply Chain, you gain access to a team of experts dedicated to solving these common warehouse challenges. Our holistic approach considers your unique business needs, industry regulations, and future growth plans to deliver pallet racking solutions that drive efficiency, safety, and profitability.
How can reader avoid problem or implement solution
To avoid common pallet racking pitfalls and implement effective solutions, consider the following steps:
- Conduct a thorough analysis of your current and projected inventory needs.
- Assess your warehouse space, including ceiling height and floor load capacity.
- Review your material handling equipment and processes.
- Consider your inventory turnover rates and picking frequencies.
- Evaluate your current safety protocols and identify areas for improvement.
- Analyze your workforce efficiency and identify bottlenecks in operations.
- Consider future growth plans and how they might impact storage needs.
While these steps provide a starting point, navigating the complexities of pallet racking optimization can be challenging without expert guidance. This is where MacMillan Supply Chain Group comes in.
Our team of experienced professionals can help you:
– Design a customized racking solution tailored to your specific needs
– Implement cutting-edge inventory management technologies
– Develop comprehensive safety and maintenance programs
– Optimize your warehouse layout for maximum efficiency
– Train your staff on best practices for racking usage and safety
Don’t let inefficient storage hold your business back. Contact MacMillan Supply Chain Group today for a free consultation. Our experts will assess your current setup and provide tailored recommendations to transform your warehouse operations. Let’s work together to unlock the full potential of your storage systems and drive your business forward.
Call us at 416-941-2759 or visit www.macmillanscg.com to schedule your consultation and take the first step towards warehouse optimization.
FAQs
Consider your inventory characteristics, turnover rates, available space, material handling equipment, and future growth plans. MacMillan can help assess these factors and recommend the best system for your needs.
Conduct visual inspections weekly and professional inspections annually. MacMillan offers comprehensive inspection services to ensure your racking remains safe and compliant.
Yes, systems like cantilever racking can accommodate irregularly shaped items. MacMillan specializes in designing custom solutions for unique storage challenges.
Signs include difficulty in inventory management, slow order fulfillment, frequent accidents, or lack of space. Our experts can assess your current system and suggest improvements.
Optimized layouts can reduce lighting and HVAC needs. MacMillan can design energy-efficient racking configurations and integrate them with smart building systems.
Essential features include load capacity placards, column protectors, and end-of-aisle guards. MacMillan can implement comprehensive safety measures tailored to your warehouse.
Modern racking can integrate with AS/RS, conveyor systems, and robotic pickers. We specialize in designing racking that complements automation for maximum efficiency.
WMS integration improves inventory accuracy, optimizes picking routes, and enhances overall warehouse efficiency. MacMillan can help implement and optimize WMS integration with your racking.
Flexible racking systems like push-back or mobile racking can adapt to changing needs. Our team can design solutions that accommodate seasonal variations efficiently.
Staff should be trained in proper loading techniques, weight limits, and hazard identification. MacMillan offers comprehensive training programs to ensure safe and efficient racking use.
Remember, MacMillan Supply Chain Group is here to answer any additional questions and provide expert guidance on all aspects of pallet racking and warehouse optimization. Contact us today to learn how we can enhance your storage solutions and boost your operational efficiency.